

Introduction to Froth Floatation
What is froth flotation? Froth flotation is a widely used metallurgical technique that is used in a variety of fields, such as mineral processing and wastewater treatment. This revolutionary technological innovation was first used in mineral processing in the early twentieth century. Metallurgy is the process of extracting a metal in its pure state from its ore on a large scale using any physical or chemical means. Metal ores are formed as a result of ore genesis and extracted through mining. Extractive metallurgy is the process of extracting important metals from an ore and refining the extracted raw metals into a purer form. Froth flotation is mainly employed for the extraction of sulphide ores.
Froth Flotation Process Principle
The froth flotation process is all about exploiting the natural hydrophobicity of liberated metals and playing with making them individually hydrophobic in order to accurately separate them from one another. The particles of metal sulphide are hydrophobic. Due to this property, they are primarily wetted by oil. The gangue particles, on the other hand, are hydrophilic and are wetted by water. As a result of stirring the solution in the tank, sulphide ore rises to the surface while the gangue particles settle. We use chemical reagents for this purpose.
Collectors: collectors in froth flotation are surfactant reagents that are used in a flotation system to convert the mineral surface from hydrophilic to hydrophobic in nature. Collectors (Xanthate) are used as a base to make metals hydrophobic (repellent to water) and allow them to attach to air bubbles.
Frothers: Frothers are what allow air bubbles to form. The froth stabilisers in the froth floatation process should be present in sufficient quantity to last until the constituent bubbles pass out of the pulp and the mineral is retained. Frothers are surfactant reagents that aid in the formation of froth. For example, pine oil, camphor oil, and so on.
Depressants and Activators: When more than one sulphide ore is present in the cell, depressants are used to depress certain minerals and promote the selective flotation of desired minerals. On the other hand, activators are reagents that improve the flotation properties of ore particles that have previously been depressed with depressants. CuSO4 is the "activator" used to prepare Zn for collector coverage.
pH Regulators: The pH of flotation is critical for selective mineral separation. The pH of a solution can be controlled or regulated by using a variety of acids and bases. pH Modifiers are used to increase or decrease the collector's water-repellency on mineral surfaces. This enables the flotation collector to act selectively on specific minerals.
Surfactants: The surface of the solid to be floated must have some hydrophobic characteristics. If not, it must be treated with specific chemical reagents to achieve hydrophobicity. Surface active agents or surfactants are the names given to these reagents. Surfactants are absorbed at the mineral-water interface, making the surface of selected minerals hydrophobic in nature.
Froth Stabilisers: Froth stabilisers are reagents that are used to extend the life of the froth (to keep it from dissolving in the solution again). A few examples of froth stabilisers include aniline, cresol, and others. Collectors and frothers are both heteropolar in nature. Their primary distinction is their affinity behaviour. Collectors' polar groups are drawn to mineral ores, whereas frothers are drawn to water only.
Froth Flotation Method
Let us now explain the froth flotation method. Sulphide ores are the types of ores that can be concentrated using the froth flotation method. PbS (sulphide galena) and ZnS are the two examples (zinc blende).
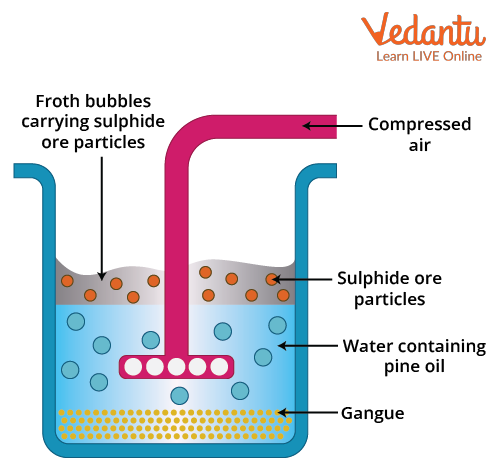
Froth flotation diagram
The sulphide ore collected from the Earth's crust is first ground to powder. This is referred to as crushing. The powdered ore and water suspension (not a solution because the ore is not soluble) are then prepared and placed in a large tank (cell). The collectors and froth stabilisers are gradually added to it. Collectors begin to encircle each ore particle. The entire suspension is agitated by a rotating paddle, which is known as the impeller. The ore particles are contained in oil froth. It floats to the surface because it is lighter than the impurities. Finally, the froth is skimmed and dried in order to recover the ores. Impurities that remain in the tank water are also collected separately.
Conclusion
In mineral treatment and mining, the flotation process concentrates the metal-bearing minerals in an ore. The crude ore is ground into a fine powder and combined with water, frothing reagents, and collecting reagents. When air is blown through the mixture, mineral particles cling to the bubbles, causing them to rise to the surface and form a froth. Gangue (waste material) settles to the bottom. The froth is skimmed off, and the water and chemicals are distilled or otherwise removed, resulting in a pure concentrate.
FAQs on Froth Flotation Principle and Process - Important Topic for JEE
1. What is the significance of frothers in the industry?
The mining industry recognises the importance of frothers in mineral flotation. Frothers enable froth formation by perfusion of the liquid-gas interface. The following key functions in the froth flotation process are hampered. Frothers reduce surface tension to keep the size of bubbles stable. Frothers aid in the adhesion of hydrophobic particles to air bubbles. Frother chemicals are typically heteropolar surface-active organic surfactants with well-balanced hydrophile-lipophile properties, branched hydrocarbon radicals, and the ability to form loosely packed gaseous films at the liquid/gas interface.
2. What is the role of adsorption in the froth flotation process?
Sulphide ore is shaken with pine oil and water in the froth floatation process, and the ore particles are adsorbed on the froth that floats, while the gangue particles settle down in the tank. Adsorption's role in the froth floatation process can thus be understood as the following processes:
Pine oil adsorption on sulphide ore particles.
Emulsion formation takes place.
Froth is formed in conjunction with ore particles.
Mechanism of shape-selective catalysis operation.
Since sulphide is extracted using the froth floatation method, only sulphide ore particles will exhibit this type of adsorbing tendency.

















